- I recommend the Pixel 9 to most people looking to upgrade - especially while it's $250 off
- Google's viral research assistant just got its own app - here's how it can help you
- Sony will give you a free 55-inch 4K TV right now - but this is the last day to qualify
- I've used virtually every Linux distro, but this one has a fresh perspective
- The 7 gadgets I never travel without (and why they make such a big difference)
Digital transformation never stops at IBM’s semiconductor plant in Québec

Technological innovation is at the heart of IBM Bromont. Founded in 1972 to meet the needs of the Canadian computer market, the plant has evolved over the years to climb the hierarchy of the computer behemoth – setting itself apart from competitors who have fled North America to Asian countries in the last decades.
Today, IBM assembles and tests its semiconductor solutions in the quaint town of Bromont, an hour from Montréal, and provides services to clients – notably in the telecommunications industry.
[ Lisez la version française : « À l’usine de semi-conducteurs d’IBM au Québec, la transformation numérique est permanente » ]
For employees using new technologies daily at the plant, the work can resemble a children’s party in a toy store: while some CIOs struggle to initiate a digital shift, the transformation at IBM-Bromont is never-ending.
“It’s been 50 years of reinventing and adapting the plant,” Louis Labelle says, executive advisor at IBM Canada and chief officer at Bromont from 2012 to 2022. IBM Bromont’s products and services are only part of the plant’s innovation. Under the guidance of its leaders, many IT solutions are developed and used on-prem continuously to improve processes and optimize operations of the plant itself.
AI: The cream of the crop
Louis Labelle, executive advisor at IBM Canada
Courtesy IBM
More than 100 million organizations around the world use IBM Watson technology when it comes to implementing AI solutions. No wonder artificial intelligence is in full swing at Bromont: “We sell what we use, and we use what we sell,” Labelle says.
“We have access to the full portfolio of IBM solutions,” says Stéphane Tremblay, the plant’s current chief executive. Among the latest tools, Bromont is using IBM Maximo Visual Inspection – an image recognition technology used to inspect micro-welds on the assembly line – and IBM Maximo Health, which “listens” to the noise emitted by the equipment to detect the slightest malfunction before it occurs.
“We also use AI for the supply chain,” Labelle says. IBM Supply Chain Intelligence Suite makes recommendations to the plant analysts about what purchases should be made.
This tool is particularly important in a context of supply scarcity, since it can suggest that a purchase be made earlier than usual when procurement lead times are longer – as is the case with the current pandemic and international crisis. Supply Chain Intelligence even allows for variations in sourcing when alternatives exist.
“Since we’re at IBM, we can use these systems as soon as they become available and quickly train our staff on them,” Tremblay says. “It’s very motivating for employees to contribute to the development of innovative projects like these.”
As with all companies in the industry, recruiting new employees is proving more difficult than it used to be for IBM – even though the plant is located in the heart of a talent pool – with the University of Sherbrooke nearby among others.
“We’re able to meet our needs, but we have to work twice as hard to get there,” Labelle says. Projects like the ones IBM continually puts in place can help tip the balance, he adds.
Mobility: a super tablet for everyone
Bromont’s IT does not innovate only with AI. With the help of the engineering department, they’ve been implementing a mobility project for the past two years in which all plant personnel – operators, maintenance employees, supervisors, and engineering departments – are equipped with state-of-the-art tablets.
“It can be used for just about anything,” Tremblay says: controlling plant equipment remotely (which increases operators’ freedom of movement), video training, filming a problem to show to another department and get help. New features are being added to those tablets all the time, even as they’re being developed by the company.
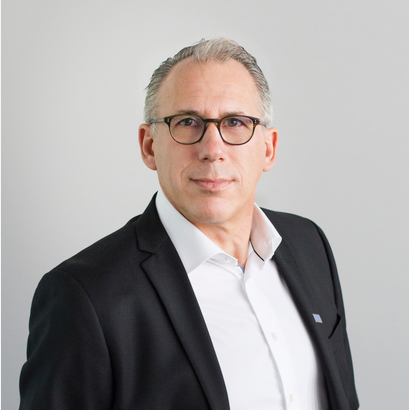
Courtesy of Stéphane Tremblay
“This journey is far from over,” Tremblay says. We’re constantly adding new projects related to employee mobility on the plant floor, such as the use of augmented reality.”
Over time, these solutions will be used in other areas of manufacturing. They will be integrated into new devices, for example for allowing access permissions to different pieces of equipment based on user types – and providing data customized to each employee.
The increased autonomy of personnel brought about by growing mobility also brings with it new challenges, including training and certification. “That’s the reality of being an operator at IBM Bromont,” Labelle says. “No one is assigned to a single piece of equipment. We train and certify our employees on an ongoing basis.”
Automation and optimization
IBM decided to stay in Bromont when all its competitors were rushing to Asia in the ‘80s and ‘90s in the hope of reducing operating costs. But for IBM, there were security issues related to the assembly of encryption systems for the company’s servers. The fact that expertise had grown at the plant over the years and that its production was constantly diversifying also weighed heavily in the computer giant’s choice.
“That’s when developing more automated solutions became an economic necessity,” Tremblay says.
Many of the operations performed at Bromont were also automated due to technical needs: “We put together semiconductors: there are components that are much too small and require way too much precision to be manufactured by humans,” Tremblay says.
So, the future of the plant sits squarely in Industry 4.0 – the “fourth industrial revolution.” IBM Bromont is striving to reuse the data collected during its operations to reinject into its processes. The goal is to increase productivity and perform continuous self-correction. “All of our equipment is connected, which means that our IT teams have access to an incredible wealth of data,” Labelle says.
The joint development of process optimization – which involves both manufacturing and engineering teams – can’t happen overnight. “Data reinjection is not yet deployed everywhere, but our teams are working on it relentlessly,” Labelle says. With the labour shortage we’re experiencing right now, this recycling is now required for optimal operations.”
On the brink of tomorrow’s computing
Another major project is taking shape in Bromont: jointly with the government of Québec, the plant announced this year that it will house a Quantum System One – IBM’s first quantum computer in Canada. “Our mission is to ensure its maintenance and proper operation,” Tremblay says.
Again, this futuristic technology will require adaptation, training, and certification by IT teams. Training will not only be given to the plant’s employees but also to other companies and to the Québec academic sector: the Quantum System One will be the core of the Québec-IBM Discovery Accelerator, intended to establish a quantum innovation zone in the province and to shape IT’s future.
For example, the plant’s quantum system will be used to model new materials and employ new digital technologies for sustainable development, drug discovery and high-performance computing.
Translation by Daniel Pérusse