- I recommend the Pixel 9 to most people looking to upgrade - especially while it's $250 off
- Google's viral research assistant just got its own app - here's how it can help you
- Sony will give you a free 55-inch 4K TV right now - but this is the last day to qualify
- I've used virtually every Linux distro, but this one has a fresh perspective
- The 7 gadgets I never travel without (and why they make such a big difference)
IT supply issues have organizations shifting from just-in-time to just-in-case buying
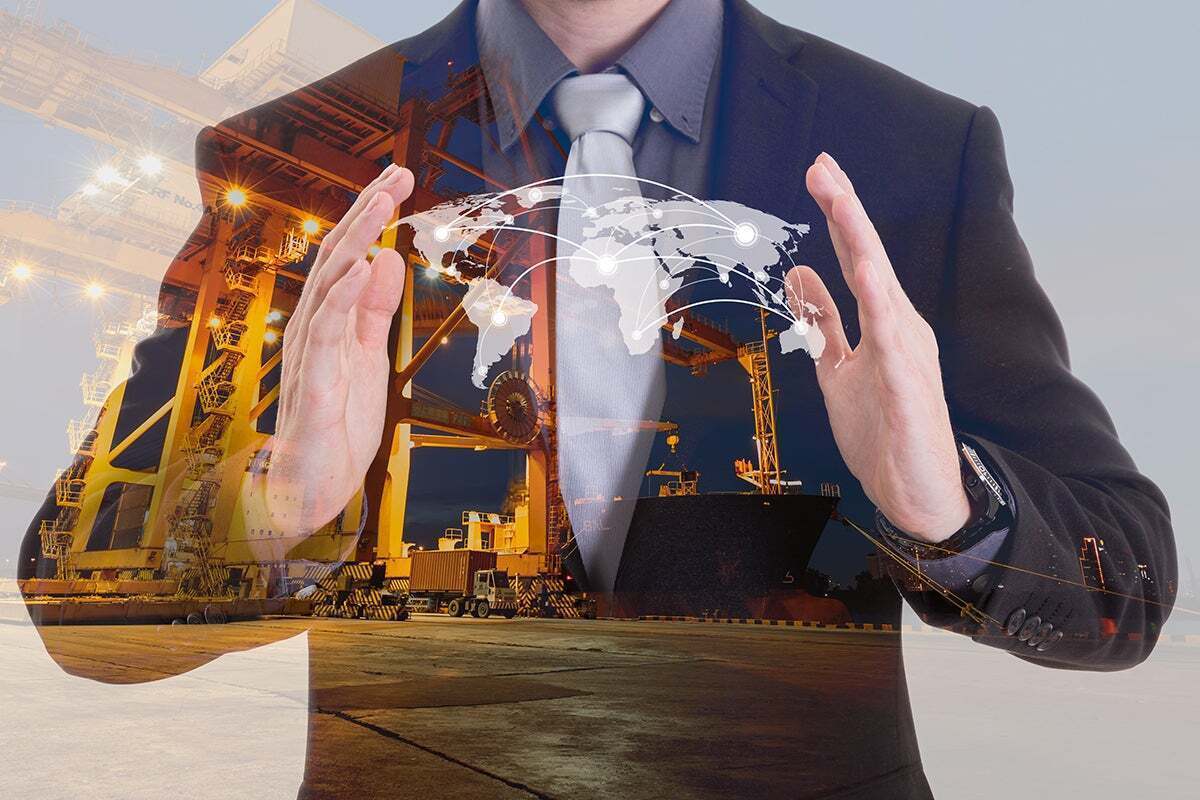
The past three years have been an unprecedented period of disruption in the semiconductor industry. The Covid pandemic and ensuing lockdowns shut down manufacturing, there were interruptions in shipping, and then the war in Ukraine adversely impacted supplies of critical raw materials.
The first half of 2022 saw 46% more supply chain disruptions than the first half of 2021, according to a research report released this fall by Resilinc, a supply chain resiliency company.
2023 looks like it might be a little bit better, in some sectors. Consumer demand, for example, is down due to inflation, rising interest rates and reprioritization of consumer spending. So networking equipment that serves both consumer and enterprise needs may become more widely available.
Meanwhile, enterprises are continuing to make strategic investments in order to support their work-from-home employees, business expansion plans, and digitization efforts, according to Gartner analyst Richard Gordon.
When it comes to some of the chips used in networking equipment, availability has improved, said Jason Bohrer, executive director at the Secure Technology Alliance, an industry group which counts several semiconductor manufacturers among its members. “They’re starting to see lead times come down,” he said. “But while the situation has improved, it’s not fully resolved.”
For chips that go into consumer electronics, lead times are no longer in the nine- to 12-month range, he said, but are more in the two- to three-month range.
Still, there are some types of semiconductors that are experiencing shortages, experts say, such as older and lower-end types of chips, as well as specialized and custom chips. That includes some boring – but critical – components, such as power supplies and printed circuit boards, said John Waite, vice president for global supply chain at professional services firm Genpact.
Even companies like Cisco, which basically has its own fabless semiconductor company, still need those components, Waite said. “It’s got to go into a chassis. It’s got to have a power supply. It’s got to have a cooling unit. Custom analog and digital parts are still constrained.”
Networking equipment manufacturers tried to address the problem by buying as much as they could, wherever they could get it, and now that deliveries are starting to arrive, they’re discovering they have too many of some components and not enough of others.
“We’re working with one large network provider with multi billions of dollars of nearly finished assets,” Waite said. They’re just missing one or two critical components that they can’t get.
“Every customer is still waiting for that one final part to finish their finished goods,” confirmed Peggy Carrieres, vice president for global sales enablement and supplier development at Avnet, a distributor of electronic components.
Exactly which parts are still missing changes day to day, she says, but, in general, microcontrollers have very extended lead times, as well as military-rated products. “Any differentiated product,” Carrieres adds.
In a survey of the electronics and components industry the company released in November, 59% of engineers say the components shortage has become more severe since 2021.
Carriers expects to see lead times coming down next year, but prices are going to continue to go up due to the cost of raw materials and the cost of labor. “Hardware engineers are still in short supply,” she says.
Onshore production a long-term play
For networking vendors specifically, the supply chain situation continues to improve, said John Abbott, principal research analyst at S&P Global Market Intelligence. “Vendors have reviewed and optimized their strategies using techniques such as demand steering and multi-sourcing, while building greater visibility and trust into their supply chains,” he said.
However, the underlying problems have not been resolved. These include national security concerns as well as supply-chain bottlenecks made worse by geopolitics and natural disasters. These problems are threatening to affect global trade.
Government investments and industry partnerships are fostering a return to onshore manufacturing, with significant investments in local manufacturing, Abbott said. “As a result, capacity will increase over the next few years.”
However, in the near term, this isn’t a solution. It can take several years for an advanced fab to come online. Plus, new investments focus on advanced chip manufacturing instead of on older designs. But the older-generation components are still important for some types of equipment.
Networking vendors report growing sales, high backlogs
“We are encouraged by what we are seeing,” said Cisco CEO Chuck Robbins at a November conference call with investors.
Robbins said that there are “modest improvements” in the availability of some components and that shortages are continuing to ease. “The redesign of many of our products has also helped bring supply stability and more resiliency,” he added.
Meanwhile, demand is high, he said, resulting in the largest quarterly revenue in the company’s history and causing the company to raise its outlook for the full fiscal year. Cisco saw particularly high demand for purchases related to secure agile networks and optimized application experiences.
“Networking is becoming increasingly critical to every organization, led by digital transformation, hybrid cloud, AI, and ML workloads,” he said.
Backlog continues to far exceed historical levels, said Cisco CFO Scott Herren, but as the company continues to navigate the complex supply environment, it was able to increase shipments and lower backlog by 10% last quarter.
Rival networking vendor Juniper reported similar results in October.
“Our backlog remains elevated, but declined sequentially due to improvements in supply,” said Juniper CFO Ken Miller. “We would expect the backlog to further decline as supply improves.”
However, 2023 will continue to be a very challenging environment when it comes to the supply chain, he said, and very unpredictable. The company currently ships products several months, or even quarters, after the orders come in. “The vast majority of our customers are trying to get the product quicker than we’re currently able to deliver,” said Miller.
What should enterprises be doing?
For some types of purchases, enterprises can ease back on the panic buying, says Mike Burns, chairman and co-founder of Pennsylvania-based iDEAL Semiconductor and managing director of Murray Hill Group, a venture capital and private equity firm specializing in semiconductors and other advanced technologies.
“There’s probably an opportunity to delay purchases involving desktop computers, notebook computers and other products that are dual use – consumers using them as well as the enterprise,” he says.
The Covid peak is going down, and enterprises should now be able to avoid pre-ordering, he says, “Just buy the best deal as the year progresses.”
Unfortunately, that’s not the case for servers and networking equipment. “For server and networking infrastructure, we’re still seeing long lead times,” Burns says. “So it’s prudent to make predictions and buy ahead of time.”
For some equipment, lead times are still several months to a year, he says.
Enterprises are also making larger orders than they normally would, says Doug Palmer, supply chain practice lead at Booz Allen.
They’re placing large “lifetime buy” or similar orders, Palmer says. “These types of orders are somewhat less common due to the up-front capital expense, but recent disruptions have acutely demonstrated the importance of supply chain risk management.”
Organizations with highly complex and interconnected networks and systems, such as large data centers and cloud providers, have been particularly affected because they’re less able to substitute components or devices, he says. The same is true for high-security applications, such as the financial services industry.
In the future, government and private investment in domestic semiconductor manufacturing should help reduce the potential for supply chain disruption. But, other than buying ahead in bulk, there’s not much else these types of enterprises can do in the short term because they’re unlikely to make wholesale changes in product roadmaps, Palmer says.
This approach is a departure from the previous common practice of just-in-time inventory management, which allowed companies to reduce their inventories to the bare minimum, but only worked when they can be sure that supplies will arrive exactly when they need them.
Just-in-case is the reverse of that – keeping larger inventories of equipment on hand, just in case it is needed.
According to an SAP SE survey released this October, 64% of companies are moving from a just-in-time supply chain to a just-in-case supply chain as a result of the recent disruptions.
When possible, enterprises can also try to diversify their supply chains and business processes to mitigate risk, says S&P’s Abbott. In addition, he recommends forming closer partnerships with key suppliers and distributors to ensure availability and working around unavoidable shortages through re-design.
It may also be time to rethink the deployment model.
“System infrastructure shortages are already resulting in an accelerated shift to the cloud,” Abbott said.
Cloud capacity is more easily available, he said – and is likely to remain that way because of the buying power and internal manufacturing capabilities of the large hyperscalers.
“The hyperscalers are going to have more leverage getting stuff,” confirms Tom Coughlin, IEEE fellow and president of consulting firm Coughlin Associates. “If what you’re involved in is being done mostly in the cloud, it will be less chaotic there.”
There are still organizations that need to run their own networking infrastructure, he adds. “But remote work, remote collaboration, and Covid have accelerated cloud-based applications,” he says.
There’s also been an increased move towards hardware as a service, says Forrester analyst Glenn O’Donnell. “The networking vendors were slower to jump on board but they’re all there now,” he says.
By getting their hardware under a subscription model, a capital expense becomes an operating expense, he says, which can be simpler for companies.
“It’s not necessarily cheaper but it’s easier to manage, especially when you have your own demand ebbing and flowing,” he says. “You’re basically paying for what you use, and if you have to lay off 20% of your staff tomorrow, your costs go down by 20%.”
Plus, it helps insulate companies from supply chain issues, he says.
Visibility key to long-term supply chain management
One thing more enterprises should be looking for is greater visibility from their suppliers.
“A lot of people are realizing that we’re living in a more transparent world now,” said Genpact’s Waite. And integration between companies has increased, with some providers offering more information to their customers.
This is particularly important for enterprises doing cognitive sourcing, he says. With this approach, vendors are selected not just based on technical fit, form, and function but also based on where in the world they source their materials, or how big of a company they are.
Supply chain visibility is particularly important for manufacturers. They need to know if the supplies they need are on track, or if alternate sources have to be found in order to avoid production delays.
“Our supply chain is built entirely on transparency,” says Carl Nothnagel, COO at specialty hardware manufacturer MBX Systems. “With every supplier, we push for that information. Sometimes we don’t get it, and we’re left with projecting, or guessing as best as we can. We have some manufacturers that are very transparent and we can see where it’s going to hit every day, and some are a bit of black hole.”
Over the last two years, transparency has decreased, he says, but he expects the situation to turn around. “Over the next few years, it will become more and more transparent. I think it is a bit of a requirement for everyone to know this information.”
Unfortunately, in today’s seller’s market, the leverage to demand better data is not there. But if the economic downturn continues, power may return back to the buyers, says Forrester’s O’Donnell.
Visibility has actually gotten worse since the start of the pandemic, he confirms. “Some of the suppliers have not been transparent because they’re trying to make the problem look less than it is,” he says. “They’ll say, we can get anything you want, we’ll take care of you – and sometimes they can’t.”
As the economy turns south, equipment suppliers will become more eager to bargain. “That’s always the silver lining in an economic downturn,” he says.
Finally, there’s some good news from SEMI, the global industry association representing the semiconductor design and manufacturing supply chain.
According to a report released in December, the worldwide semiconductor industry started work on 33 new chipmaking facilities this year, a record high. And between 2021 and 2023, the industry is projected to invest more than $500 billion in 84 volume chipmaking facilities. Among them are 18 new facilities in the Americas and 17 in Europe and the Mideast.
Unfortunately, the bulk of new investments are for the most advanced chips, says Mirko Woitzik, global director of intelligence solutions at Everstream Analytics. “But it is precisely those chips that are facing the lowest market demand currently,” he says.
Lagging-edge chips, which include micro control units as well as analog, discrete power, and logic sensors are being left behind. “Chip makers have been very reluctant to dedicate new fab capacity for lagging-edge chips,” says Woitzik.
Copyright © 2023 IDG Communications, Inc.