- I ditched my daily driver Bose headphones for the XM6 - and I'm hesitant to go back
- This Lenovo ThinkPad is my top pick for remote work - and it's nearly 50% off now
- I invested in this 3-in-1 robot vacuum, and it's paying off for my home
- I've tested the Meta Ray-Bans for months, and these 5 features still amaze me
- My new favorite iPhone portable charger has a magnetic superpower - and it's cheap
Manufacturing CIOs see bright future for the industry, thanks to IT

The manufacturing industry is undergoing a renaissance, thanks in part to advances in information technology. Two IT leaders who have been on the forefront of that are Kim Mackenroth and Chris Nardecchia.
Kim Mackenroth is vice president and global CIO of Textron, a Fortune 302 multi-industry company with around 33,000 employees worldwide. Her global IT organization comprises five business-segment CIOs, as well as shared services provided by the CISO, CTO, and the leader of enterprise business systems. CIO 100 award-winner Chris Nardecchia also wears multiple leadership hats in his role as senior vice president and chief digital and information officer of Rockwell Automation, the world’s largest pure-play industrial automation and IoT company.
These two industry leaders have much in common, from their parallel career paths to their leadership philosophies and experiences. When the three of us spoke for a recent episode of the Tech Whisperers podcast, we explored how Mackenroth and Nardecchia are succeeding with their transformation journeys, winning with people, and not only answering the CEO’s call but also changing the IT narrative to get those calls in the first place. Afterwards, we spent some time talking about their career journeys and the technology that excites them about the future of manufacturing and business. What follows is that conversation, edited for length and clarity.
Dan Roberts: You have similar career stories in that neither of you started out in IT and never intended to get into this profession. Where did you start, and how did you get here?
Kim Mackenroth, vice president and global CIO, Textron
Textron
Kim Mackenroth: I believe a career path is not a ladder but a jungle gym of experiences — some lateral, some vertical — that provide a solid foundation for the ones that follow. While I never intended to be a CIO, I have always had the philosophy of ‘take the role that scares you the most because that is where you will grow the most.’
Throughout my career at Textron, I have had many roles, spanning supply chain, manufacturing, integrated product teams, and working on helicopter programs. There was an opportunity to be part of a new way of conducting business at our Bell business unit, so I took that role, and as a result, the CIO took notice and asked me to join his organization as a direct report. He rotated me throughout IT, and then I became a CIO of two other businesses prior to becoming Global CIO.
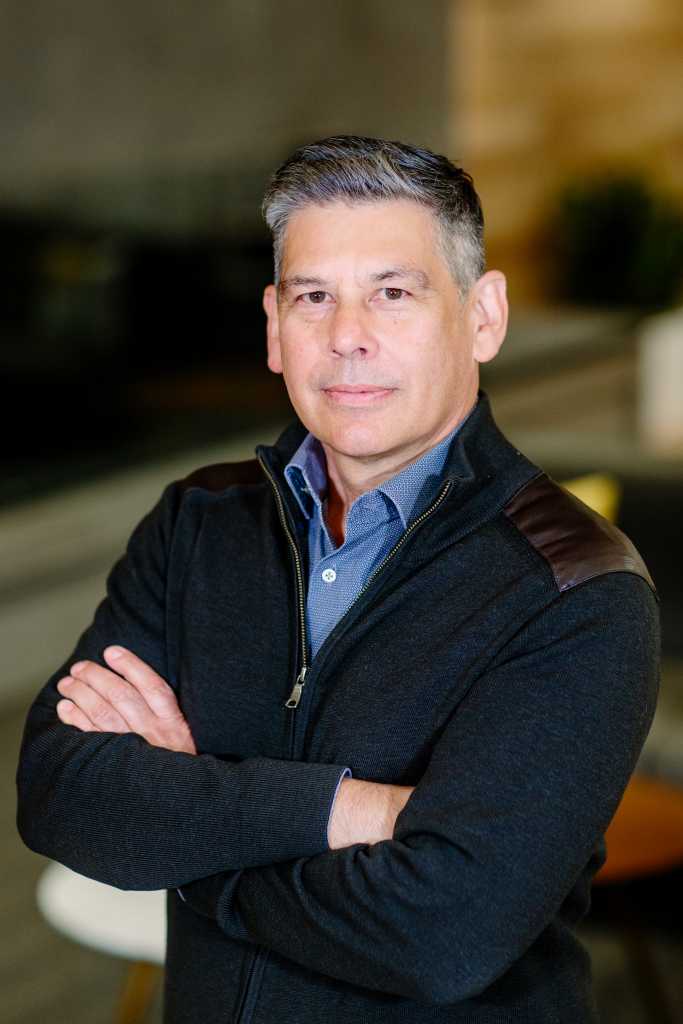
Chris Nardecchia, SVP and chief digital and information officer, Rockwell Automation
Rockwell Automation
Chris Nardecchia: I started as a chemical engineer doing chemical engineering things, building and operating chemical and nuclear processes, producing polymers and nuclear fuel, etc. That led me into a role in the pharmaceutical industry, again, building and operating processes to manufacture pharmaceuticals. As part of that role, I got involved with computer control of manufacturing processes, and that’s when I started to code. That then led to an increasing involvement of trying to move data across the enterprise to compare manufacturing operations around the world.
During this period, when we were expanding at a rapid pace and building new manufacturing plants around the globe, I was approached by the head of our manufacturing division to lead the implementation of SAP across our manufacturing network. I realized it was career-limiting to tell the president of a division ‘no,’ and that started my journey into IT.
From that point forward, I was fortunate enough to lead both the IT and OT teams within global pharmaceutical manufacturing and supply chain organizations. Those experiences prepared me well for what Rockwell Automation needed in their next IT leader — someone who can not only run the IT operations but also understand manufacturing in the OT environment.
Dan Roberts: I recently spoke with Charlie Feld, who said that, before the internet, we had more time to build relationships and to think. But we also we didn’t have the technology to do all these great things we’ve come up with since. What technology are you most excited about now and as you look to the future?
Kim Mackenroth: Earlier in my career, I worked at Bell’s drive systems center, where we build all the high-tolerance parts for our complex gearboxes that go into our helicopters. We had large batches of parts, which would have to get through an enormous amount of processing, machines, and external providers to complete. We used to say they travel many miles to hopefully yield the parts that we needed for assemblies.
We had a dream at that time: Wouldn’t it be great to live in this world where we could have one piece part flow. Where we could have machines that were capable of digital loops where they could adapt, they could produce a quality part every time, they could do multiple operations, they could significantly reduce the amount of equipment that was required, the number of operations and the amount of span time.
Bell now has a manufacturing technology center — a purposeful factory of the future. It was all about creating and testing the capabilities that I just talked about, and how to embed that back into our core manufacturing processes. Everything that I just described is happening, and it’s the culmination of engineering, manufacturing, modern machines and software, all coming together to yield the future we dreamed about.
Chris Nardecchia: Those things really excite me. We’re clearly in the age of AI. We’ve seen the amazing progress with open-source AI, with ChatGPT, and previously with DALL-E. This is just the tip of the iceberg. Applying similar capabilities to manufacturing, as Kim just went through, is in progress, and it’s just going to accelerate. I’m extremely excited about the exponential impacts that applying these technologies can have on manufacturing operations.
To cite just a few results that have been achieved with digitization at Rockwell, we’ve seen a 40% improvement in quality, a seven-figure improvement in productivity, and, prior to recent supply chain issues, our on-time delivery improved from 82% to 96%. These are big numbers, but imagine what the possibilities are when you apply advanced AI algorithms.
Here’s a real-life example at Rockwell. Part of our manufacturing process is to create electronic components with circuit boards, and you embed computer chips in them. We have six plants with 24 manufacturing lines and 50 machines that contain 2,000 nozzles that place these chips from a spool at a very high speed onto the printed circuit board. The exact placement on that board is critical. If you get these off a few millimeters, then you’re scrapping boards.
Over time the nozzles can wear out and drift away from the proper location. To avoid bad boards being created, we used to perform maintenance on a time schedule, and we’d frequently replace good nozzles that still had life in them. Now, we replace them just before failure by leveraging an AI solution that predicts the drift of these nozzles at very high speed and notifies the operator via a visual application when they’re predicted to fail.
At a cost of $5 to $500 per nozzle, it saves significant costs, but more importantly, it maximizes the machine utilization and uptime. This is just one example. If you think about the countless manufacturing lines across the world, there’s just huge opportunities.
Roberts: Kim, you talk about software like driving a car. What do you mean by that?
Mackenroth: Everything was previously hardware-centric. It’s like in the example that Chris gave, we had those windows of opportunities where we’d replace hardware because the source of the world was hardware. Now, software eats hardware for lunch.
Look at Tesla. When you get into a Tesla, it’s not all the bells and whistles from a hardware perspective. That’s not what it’s about. It’s about that software experience — having those monthly updates, getting the new features and functions. Probably not the most comfortable seat, not all the little ecosystems that you would have in a luxury vehicle, but the enthusiasm is off the charts because of that customer engagement, that customer experience of, what am I going to get next? What am I going to be able to do next? None of that could have been accomplished with the previous automotive industry approach.
Roberts: Back in the day, we used the phrase eating our own dog food — or drinking our own champagne. Chris, you talk about it as Rockwell on Rockwell. What does that look like?
Nardecchia: The concept here is borrowed from the software world where we use our own products and our own solutions and our own manufacturing facilities, not only to improve our own operations, but to showcase them for our customers. So in our manufacturing headquarters today, where there previously wasn’t any manufacturing because everything shifted overseas, we’ve now brought back manufacturing and demonstrated in almost a lights-out facility, one operator, all the technology advancements that people can apply.
This is us walking the talk, not only with our own products but our partner ecosystem so that we can feel good about what we’re promoting to our customers and find the flaws of the implementation experience. If the customer is going to experience this, we want to experience it first and then modify what that experience is for the end customer. Demonstrating these capabilities in our own four walls allows us to speak about them with conviction with our customers.
Roberts: Is there going to be a manufacturing renaissance in the US?
Nardecchia: I think it’s happening and it’s driven by two or three things. One is the supply chain and the geopolitical events that are happening. That’s awakened people to say, ‘What do we do and how do we secure our supply chain?’ It’s also driven a little bit by the labor shortage — how do we sustain a society in a growing population through automation and that marriage between machines and human intelligence? How does that work?
A number of companies that moved manufacturing to low-tax havens are now announcing facilities being built in the US in the coming year. We’re seeing the semiconductors move from Asia over to the US. We’ll have to see if it stays and sticks, but I believe that you’re going to see more manufacturing centric in the US.
Roberts: Kim, after 27 years at Textron, what keeps you excited about what you do?
Mackenroth: I get this question a lot, and I would go all the way back to the beginning. I am so grateful for the group of leaders that brought me in at Bell where I began my career, the mentors that challenged me, and the wonderful teammates and colleagues I get to work with. There’s that phrase, ‘Hire people who amaze you and then teach them how to amaze themselves.’ I feel like Textron has done that for me, and it’s part of my legacy to those people that follow me to make sure they’re having a career journey that amazes themselves.
But there’s two big reasons why I’m here outside of all of that. I love the talent philosophy. It is rare in a multi-industry, global organization to have such a passion for developing and promoting people from within. That’s incredibly special and supports the opportunities that we can offer. My CHRO talks about community, cause, and career. That is important, but I would add people, purpose, and passion. My number one, most enthusiastic item is purpose, and if I summarize everything that we do at Textron, we literally defend freedom. We protect the warfighter. We save lives. We build time machines. We move humanity. Who else can say that?
Dig deeper into the career journeys and leadership playbooks of Mackenroth and Nardecchia by tuning in to the Tech Whisperers podcast.