- I tested a Pixel Tablet without any Google apps, and it's more private than even my iPad
- My search for the best MacBook docking station is over. This one can power it all
- This $500 Motorola proves you don't need to spend more on flagship phones
- Finally, budget wireless earbuds that I wouldn't mind putting my AirPods away for
- I replaced my Linux system with this $200 Windows mini PC - and it left me impressed
Outsourcing vs. DIY: Monitoring and Servicing Critical IT at Edge Computing Sites
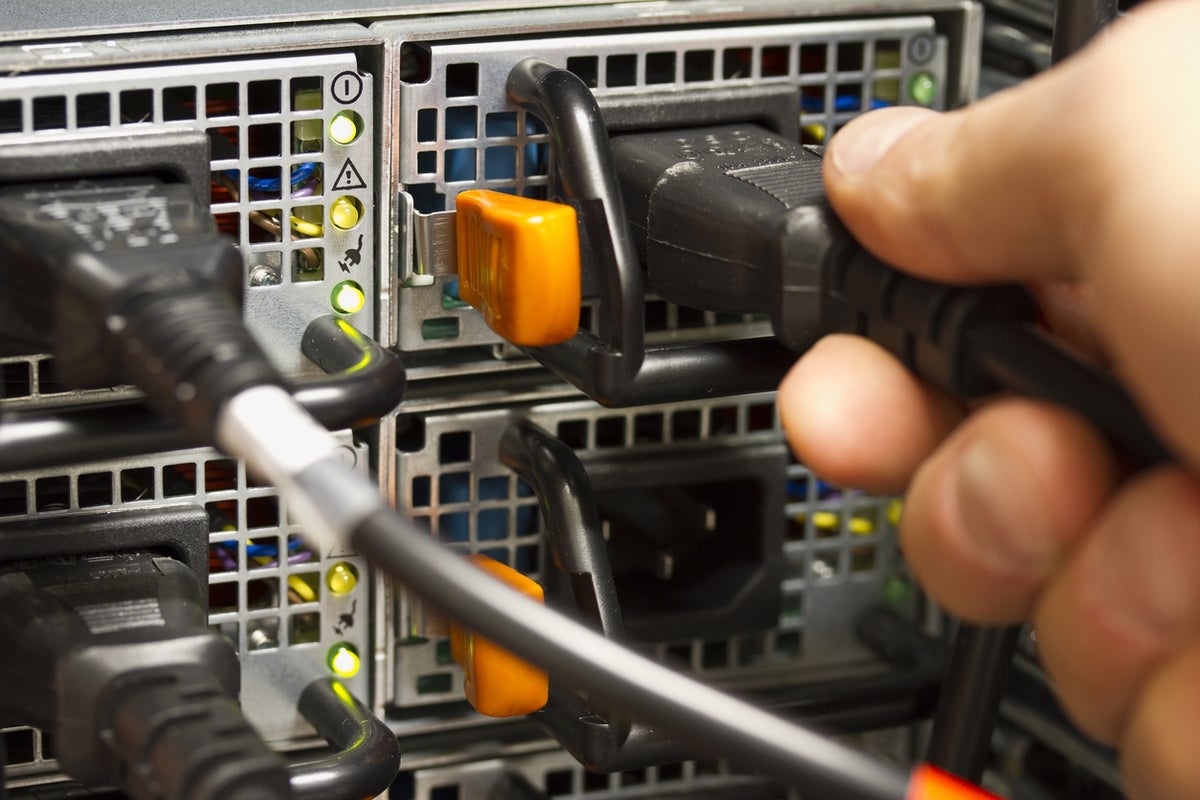
Monitoring and servicing are two critical functions to ensure your distributed UPS assets do the job they were intended to do to keep your critical edge computing applications available. But when you have UPSs distributed across dozens, hundreds, or even thousands of sites, managing them can be a challenge due to the geographic dispersity, the lack of trained/dedicated staff, and the mixed ages/models of the fleet.
Some companies opt to manage their fleet themselves, while others choose to outsource the functions to a 3rd party vendor or partner. There are both qualitative and quantitative trade-offs involved when deciding which approach makes sense for you. I recently published a white paper to discuss these monitoring and servicing considerations (White Paper 283, A Quantitative Comparison of UPS Monitoring and Servicing Approaches Across Edge Environments), but will summarize them here…
Monitoring considerations
There are three important factors to consider regarding monitoring your UPS fleet on your own.
- Digital capabilities – is each of your UPSs connected to the network (i.e., through NMC cards)? Although the UPSs are connectable, they are sometimes not actually connected due to lack of resources and knowledge about the UPSs at the sites.
- Staffing – make sure you have centralized resources (i.e., a NOC) that can be the virtual eyes on the assets 24×7. When relying on site staff to make sure systems are stable, critical alerts like a beeping UPS or a flashing “replace battery” LED may be overlooked because those site staff have other primary job responsibilities.
- Expertise– staff members monitoring the UPSs should be trained to know the appropriate actions to take when critical alarms occur.
Servicing considerations
Likewise, there are several factors that may impact your decision on whether to service your UPS fleet yourself vs. outsourcing it to a partner or vendor. These include:
- Logistics of getting technicians where they are needed – It can be a cost-prohibitive logistics nightmare to get the service techs to each site for maintenance when sites are geographically dispersed. It is important to assess your capabilities of handling the fleet in a timely manner when maintenance needs arise.
- Unpredictable expenses when systems fail – Internal staff and truck dispatch costs should be well understood, so you can compare these with the cost of a maintenance contract with a partner or vendor. You also need to consider what business model suits your company best…sporadic maintenance expenses as failures or maintenance needs occur or predictable annual contract operating expense that accounts for all servicing work needed.
- Expertise & confidence of onsite staff performing work – Taking staff away from their primary responsibilities at your sites (such as selling, managing inventory) to deal with maintenance tasks like swapping out a bad battery has both an opportunity cost that should be understood, as well as a downtime risk if the staff member isn’t overly familiar with the system they work on. Assess these costs and risks before deciding on the servicing approach.
- Mixed age fleet complexity – Typically, a fleet is of mixed age, ranging from new UPSs to ones approaching end of life. They may also be different model / size UPSs. This can make understanding the maintenance needs challenging. DCIM can help by providing an aggregated dashboard view of the fleet and alerting you with prioritized maintenance activity.
- Access to parts – Servicing the fleet yourself means managing the access of the necessary parts. It’s helpful to have regional distribution centers with spare parts to enable faster procurement.
A tool to compare the opex
Understanding the cost implications of this decision can be complex. We developed a web-based tool called the Edge UPS Fleet Management Comparison Calculator, to help you see the potential cost differences of managing the fleet yourself vs. outsourcing those functions to a partner or vendor. It lets you input details regarding the size, number, and ages of your UPSs in the fleet, define costs associated with your internal staff and truck roll costs, as well as cost of downtime, and then contrasts that to the cost of outsourcing the fleet management. This tool can also serve as a framework for discussing the variables that impact cost.
I encourage you to access and try the tool yourself, as the answer depends largely on your particular fleet’s attributes and business costs. Outsourcing can save upwards of 40% in many cases (as the screenshot shows), but there are some cases, where the cost difference is lower. In the white paper, we explain the methodology and assumptions of the tool, and also walk through four scenarios to demonstrate the key drivers to the cost differences. Those key cost drivers are (1) age distribution, (2) cost of downtime, and (3) operating costs of managing the fleet yourself. So while the tool demonstrates that in many cases, 3rd party management is a more cost-effective alternative, I encourage you to test it out based on your own distributed IT UPS installments.
Copyright © 2021 IDG Communications, Inc.